The Intelligent Power Module, IPM, has been a mainstay in motor speed control designs. And with good reason: Such designs are relatively easy and cheap to implement. With onboard gate drivers, protection, and a six pack IGBT array integrated, it takes very little engineering effort to quickly develop an effective design. Utilizing a stamped lead frame, plastic package, and high-volume components, and given an automated production line, the IPM has all the ingredients necessary to manufacture a low-cost component solution.
However, standard IPMs are not the panacea they would seem to be. Lacking a front end converter - that is, a diode bridge array - and a PFC boost converter section, they fall far short of the mark for highly efficient, IPM-based drive designs. Vincotech has a new IPM module platform that incorporates all these sections - the flowIPM-1B. It is a complete single-component solution.
Housed in Vincotech's ruggedized, low inductance, flowPIM-1 package, the
flowIPM-1B meets the application needs of harsh industrial environments.
Architecture
Figure 1 shows the schematic of the flowIPM-1B. It depicts a complete drive solution featuring a full bridge diode converter, single boost PFC with driver and boost diode, six-pack IGBT stage with driver, shunt resistors, and thermistor.
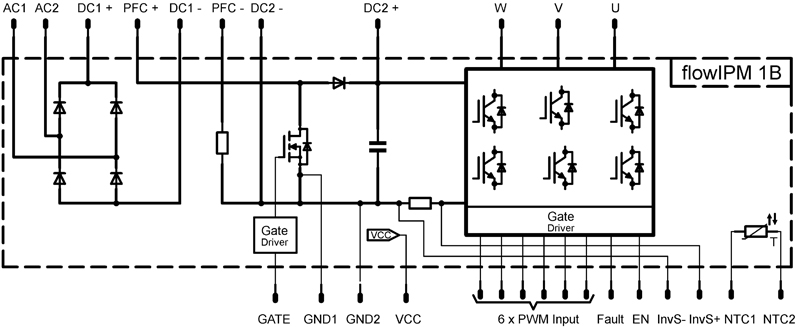
The flowPIM-1B offers considerable value and great benefits for low-power drive applications:
- Highly efficient, IPM-based drive design with converter and PFC included
- No external point-to-point connections for switching elements) and low-inductance module design, resulting in far less EMC/EMI than with a discrete solution
- Compact integrated module solution - small footprint that takes very little PCB real estate
- Highly reliable with no interconnections necessary between components
- 100% factory tested
- Reduced time to market with less time devoted to design and testing
Performance
Responding to customers' demands and insights gleaned from studies of the market for low-power drives, Vincotech now offers a full lineup of modules with various options. The ultra fast boost diode-based P953A and SiC boost diode-based P953-A10 both contain a 600V/4A/350m? PFC mosfet, utilize a 600V/4A IGBT six-pack, and address up to 1KW drive designs. The ultra fast boost diode-based P955-A and SiC boost diode-based P955-A10 use a 600V/10A/190m? mosfet alongside a 600V/10A IGBT six-pack, which increases power handling for up to 2kW designs. The switching components are enhanced with Kelvin emitters for faster switching, resulting in lower losses. In combination with a low-inductance design, these features enable the designer to employ a higher switching frequency, resulting in an application that uses smaller and fewer power components such as inductors, noise filters, and the like.
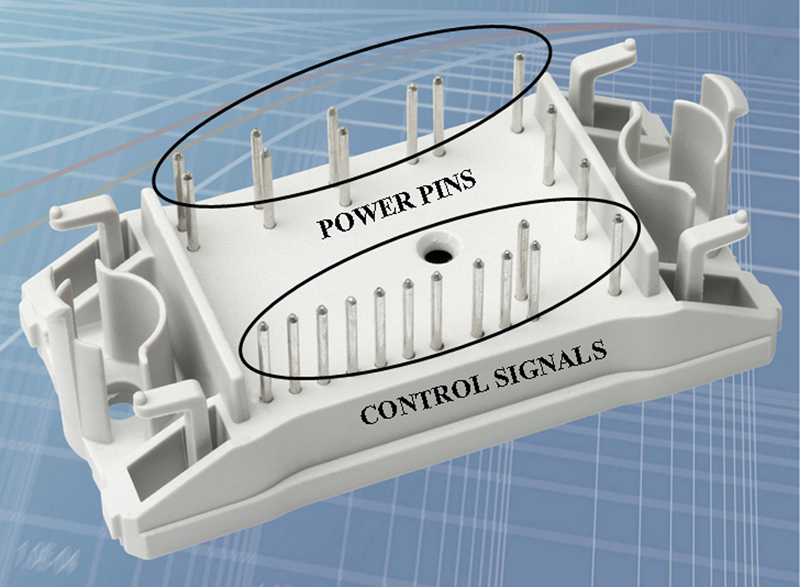
Innovative Powerflow Package Design
Vincotech engineered the flowPIM-1B pin layout specifically to facilitate PCB design. The control signal pins reside together on one side of the module. Power line pins on the opposite side of the module are grouped by functionality to create a power flow structure.
Why Power Factor?
Adding power factor to a drive design does increase system cost since it requires a few additional components such as a power inductor and additional switching elements - i.e. mosfet, boost diode. However, this small incremental cost in the drive will save the end user in both installation costs and energy savings.
Reliability
In conventional designs, high performance/ high reliability and economy are to some extent mutually exclusive. The designer is compelled to strike a balance between performance and reliability on one side of the scale and cost on the other. Obviously, the designer must factor reliability into the cost equation - the last thing a manufacturer wants are field failures, both long and short term. Modules that use a ceramic substrate solve this problem. This results in a solution that remains reliable over the long term, sparing the manufacturer costly warranty returns. Modules have fewer point-to-point solder connections which increases reliability. A low-cost, unreliable discrete design can adversely affect the manufacturer's credibility.
Lower Manufacturing Costs
Many designers choose a discrete solution based solely on the cost of components, which fails to take the total cost of ownership into account.
Discrete cost factors
- Aligning, attaching, and fastening discretes to the heat sink entails manual labor
- Individual electrical isolation material is necessary for each discrete device
- The design mandates individual heat sinks
- Using a single heat sink for discretes requires more holes
To drive down manufacturing costs for designs using discretes, Vincotech offers its new Press Pin technology on the flowIPM-1B and other modules. Modules are simply pressed rather than soldered into the PCB to reduce assembly time and costs.
Press fit pin design is well established in the automotive industry and provides a reliable and gas-tight connection to the PCB. Further advantages of press fit technology include reuse of the PCB and design flexibility. The module can be removed without damaging the PCB, thus allowing for the reuse of the PCB with a new module. Design flexibility is guaranteed by the elimination of the need for soldering; the module can easily be mounted on either side of the PCB at no extra cost or effort.
Typical Application Example
In a typical application, today's modern window air conditioner would benefit by increasing its efficiency. These are consumer appliances, so the manufacturer must pay close attention to cost. The implementation of the flowIPM-1B for the compressor motor inverter enables a universal input voltage from 100VAC ~ 240VAC. This allows the manufacturer to select a single motor for a given BTU size (up to 6500 BTUs) to cover the different voltages required in US, European, and other markets. A smaller, lighter, and more efficient motor driven by a variable power inverter replaces the standard compressor motor. Using a single motor for each model size creates economies of scale, thereby further reducing costs. And the higher efficiency rating helps differentiate the manufacturer's product from the competitors'.
Comparing Costs
Many engineers balk at the higher cost of modules over an equivalent multiple-component discrete solution. Vincotech has painstakingly qualified the components used within each module and the entire assembly to ensure it meets all datasheet specifications, including minimum, typical, and maximum values. Using a cheaper discrete part with half of the data provided certainly does not make a product more durable. Vincotech's modules are subjected to rigorous battery of specifications and functionality tests for each type of module. A discrete solution is the sum of its many individual parts, which must be tested collectively. Modules, in contrast, take the guesswork out of the topology, making the design more efficient and reliable and reducing test time during the manufacturing process. All this drives down design and manufacturing costs.
Evaluation Board
Vincotech has introduced a flowIPM-1B evaluation board to facilitate engineers' evaluation and development efforts:
-
- P950 power module featuring rectifier, PFC, six-pack with driver, and current sensing shunts
- Complete 1 kW PFC circuit with PFC controller (switching frequency settable by resistor)
- 110 VAC - 230 VAC single phase input with 2 stage EMC filter, fuse and NTC inrush protection
- 380 VDC link (settable by resistor)
- Phase 230 VAC motor output
- V TTL-compatible inverting (active low) PWM inputs for the six-pack
- Dedicated enable input (active high)
- Fault output signal (open collector)
- AC/DC converter for powering the PFC controller, measurement circuit and gate drivers in the module
- PCB designed to satisfy IEC61800-5-1, pollution degree 2, overvoltage category III standards
Conclusion
Vincotech's new flowIPM-1B module offers an innovative new way to design a highly efficient, PFC-based IPM with very little effort. The same modules, without PFC (1B06INA004SA - 1kW; 1B06INA010SA - 2kW) are also available. A manufacturer can use a single board design to offer both standard (without PFC) and premium (with PFC) drives. The single streamlined design creates economies of scale and cuts costs. Beyond that, Vincotech offers the press pin option as well as pre-applied phase change material to further reduce manufacturing costs. A full line of module-based solutions with extraordinary reliability and optional press pins and pre-applied phase change material - all this adds up to best-in-class value.
www.vincotech.com